Epoxy Coated Rebar (Reinforcing Bar)
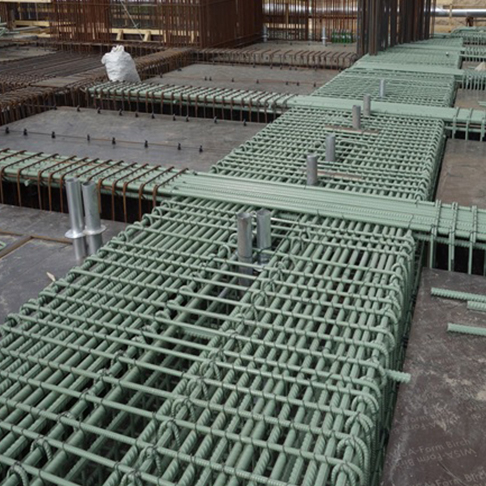
EPOXY COATED REBAR (REINFORCING BAR)
Epoxy-Coated Reinforcing Bar - Rebar for strategic infrastructures & superstructures. When miscellaneous chemicals used in strategic and qualified infra and superstructures, roads, bridges, viaducts and industrial plants and various environments and processes and natural factors such as rainwater, moisture etc. penetrate into steel fittings inside the foundation concretes, concrete platforms, concrete columns and beams which function as load-bearing components, corrosion formation occurs in these steel fittings.
Steel equipment inside the concrete construction materials bearing the columns, drums, exchanger and other steel constructions are adversely affected by rainwater, moisture and acidic or basic chemical leakages; corrosive ions carbonate the cement paste and decrease pH surrounding the steel equipment.
Corrosive ions inside the concrete deteriorate the passive film on steel equipment surface and cause corrosion.
Epoxy-coated reinforcing bar is used to strengthen the reinforced concrete construction. It is generally called as rebar abroad.
Epoxy-Coated Rebar plays a significant role in prevention of corrosion which causes cracks in concrete blocks especially in strategic and qualified infra and superstructures, roads, bridges, viaducts and industrial facilities and plants.
The worldwide accepted standard for Epoxy-Coated Rebar, namely epoxy-coated rebars, is ASTM A 775 / 775 M.
The first Epoxy-Coated Rebar had been used in 1973 in the construction of Schuyklkil bridge near Philadelphia, USA. Having been used as a basic method to protect the reinforced concrete constructions from corrosion in North America, this method is widely used in Middle East and Asian countries as well.
In USA and Europe, the use of Epoxy-Coated Rebars which are manufactured in ASTM Standards in airports and highways is stipulated in technical specifications as standard.
Places such as concrete roads, bridges, viaducts, industrial plants etc. are exposed to many natural and chemical factors such as rainwater, moisture etc. When these factors penetrate into steel fittings inside the foundation concretes, concrete platforms, concrete columns and beams which function as load-bearing components, they cause corrosion in these parts.
These corrosions decrease the Power of Hydrogen (pH) which ensures durability and surrounds the steel equipment inside the concrete construction materials bearing the columns, drums, exchanger and other steel constructions. Abrasion and wear caused by the corrosion lead to corrosion and volume expansion and cause cracks in concrete blocks, cut loss in iron equipment inside the concrete and decrease in mechanical strength and endurance against the load carried. Reparation works as a result of cracking and deformation of the concrete and new steel equipment costs would cost more especially in terms of security of life.
Thanks to Epoxy-Coated Rebar is a physical and electrochemical barrier which is formed on the steel and the equipment is isolated and protected from corrosion. For that reason, it is very crucial to use Epoxy-Coated Rebar during construction.
There are many tests performed using Epoxy-Coated Rebar throughout the world. According to these test results, Epoxy-Coated Rebar is much more durable than ordinary products. Moreover, when the cost calculation is considered, it almost returns 50% profit in the long term.
Just like the manufacturing process, the packaging and shipment processes of the Epoxy-Coated Rebar is very crucial to avoid any probable damage. Manufactured rebar products are covered with specially designed plastic packaging materials and then shipped properly. However, Epoxy-Coated Rebar to be packaged as desired in line with the qualifications of the project.
Technical Specifications
Just like dowel bars, epoxy-coated rebars are steel equipment which are used to strengthen the concrete fields and any probable corrosion.
What are the fields of use for Epoxy-Coated Rebar ?
Epoxy-Coated Rebar can be applied and used not only in concrete roads or airports but also in many different points.
Bridges and Viaducts: The bridges and concrete-covered viaducts must resist for many years. Epoxy-Coated Rebar must necessarily be used in the construction of the bridges and viaducts. Resistance against corrosion and long service life depends on the use of epoxy-coated rebars.
Power Plants: Nowadays, Epoxy-Coated Rebar is used in steel equipments of many chemical plants and power plants in Europe and America.
Dams: Epoxy-Coated Rebar is one of the infrastructure materials which are necessarily be used in the construction of dams. The corrosion progresses more rapidly within the structure of dams which are exposed to acidiferous or natural weather conditions such as water, moisture, rainwater etc. To prevent this rapid progress and to extend the service life of dams, epoxy-coated rebars must necessarily be used in the construction process.
Shopping Malls: The floors of the shopping malls are exposed to both pedestrian and vehicle traffic during the day. To ensure the long service of life, Epoxy-Coated Rebar must necessarily be used in the construction of shopping malls.
High-Rise Buildings: Buildings such as plaza, skyscrapers and residences etc. require a strong and solid foundation and infrastructure. For that reason, Epoxy-Coated Rebar must necessarily be used in the foundation of high-rise buildings.
How is adhesion of epoxy-coated rebars to concrete?
It is completely incorrect that the paint on Epoxy-Coated Rebar decreases the adhesion force to concrete. Contrary to popular opinion, epoxy-coated rebars have more adhesion force when compared to other ordinary products.
The slope of the line (tga) in elastic zone on traction – unit elongation curve is called as elasticity module E (MPa). The value of the elasticity module is determined by the initial curve of the interatomic bond-force curve. The greater the initial value of this curve, the higher the elasticity module (MPa) of that material; namely, such material is that much rigid. Otherwise, the material becomes flexible. Below table provides tensile test statistics of epoxy-coated rebar. As can be seen in MPa results, these epoxy-coated steel reinforcements have the greatest adhesion values.
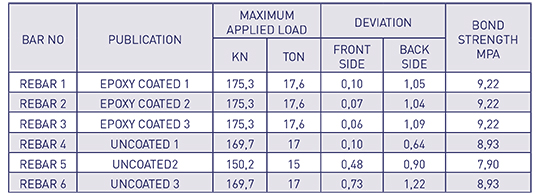